Trichlorosilane Market Outlook:
Trichlorosilane Market size was valued at USD 6.57 billion in 2024 and is projected to reach USD 20.52 billion by the end of 2037, registering around 9.99% CAGR during the forecast period i.e., between 2025-2037. In 2025, the industry size of trichlorosilane is evaluated at USD 7.23 billion.
The primary growth driver of the global trichlorosilane market is the increasing need for solar power and, particularly, photovoltaic (PV) systems. According to the International Energy Agency (IEA), global solar power capacity is likely to jump by over 610 gigawatts (GW) by 2025 due to favorable government policies and technological innovation. This increase in solar installations directly corresponds with the increasing demand for polysilicon, which is mainly manufactured out of trichlorosilane. As countries aim towards fulfilling their goals of renewable energy, the reliance on solar technology will persist in favoring the TCS market and therefore position it as an essential part of the solar cell manufacturing.
Trichlorosilane availability is based on metallurgical-grade silicon and hydrochloric acid, led predominantly by China, which is responsible for over 61% of global silicon. Price volatility, spurred by China's energy shortages in 2021–22, boosted upstream costs by 159% on the trichlorosilane price. China, Japan, and South Korea raised output by 16% across 2023–2024, with capacity additions near semiconductor and solar fabs. The U.S. imposed extra safety compliance costs of USD 3–6/ton, prompting Asia's higher imports. India's 2023 anti-dumping duties (19–23%) shifted procurement to Malaysia and Thailand. R&D costs are under national solar and semiconductor funding without line-item allocation for TCS. Trade and production line flows continue to change due to alterations in regulations and regional patterns of sourcing.
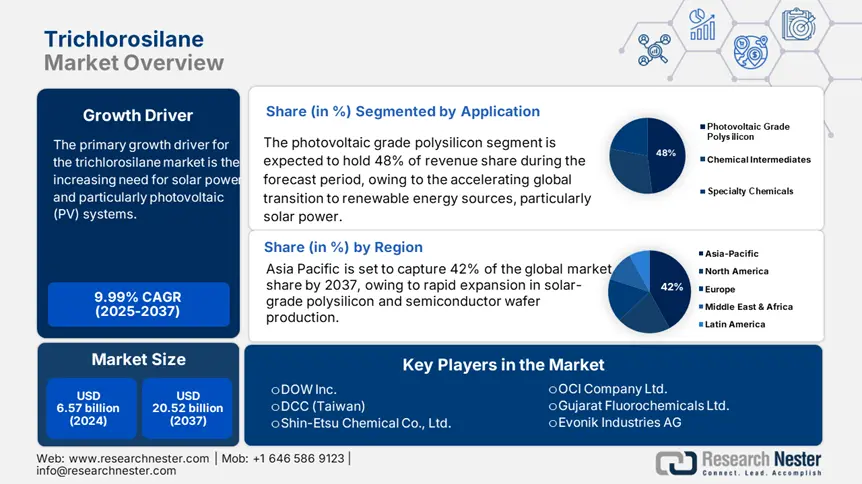
Trichlorosilane Market - Growth Drivers and Challenges
Growth drivers
- Regulatory stringency and compliance costs: Latest regulatory enhancements by the U.S. EPA and the European Chemicals Agency (ECHA) have had a significant influence on TCS manufacturing. In 2024, the EPA updated TSCA fees by lowering risk evaluation fees from USD 5.2 million to USD 4.4 million, while increasing pre-manufacture notice fees to USD 37,100, reflecting heightened regulatory scrutiny of specialty chemicals. A new Clean Air Act directive (April 2024) mandates toxic emissions monitoring at over 202 U.S. plants, contributing USD 151 M/year in compliance costs to the industry. Projecting these to chemical plants, TCS producers can likely anticipate 11–16% additional compliance overhead expenses from emissions-control retrofits, extended record-keeping, and protection of workers. These inflationary pressures on costs resulting from regulation severely impact mature plants, driving them towards modernization or relocation, thus redefining supplier relations and the pattern of demand.
- Production innovation and sustainability transition: Green process innovations and new catalysts are transforming the TCS manufacturing scene. According to EPA's Green Chemistry Program, the utilization of sophisticated catalytic systems and cleaner feedstock cycles has improved reaction efficiency by 21%, lowering energy consumption and waste streams. Concurrently, growth opportunities for the renewable chemicals industry, valued at USD 253 B by 2028 with over 12% CAGR, are fueling growth for sustainable process intermediates. Although TCS is not a renewable product on its own, its use on photovoltaic-grade polysilicon and semiconductor fabs requires compliance with Green Chemistry standards. Companies that invest in lower-carbon catalytic chlorination processes earn longer-term contracts with green-related buyers, anticipating cost savings as well as carbon-credit income.
1.Market volume and growth trends in the global trichlorosilane market
Global Trichlorosilane Production and Growth (2020–2023)
Year |
Global TCS Production (Million Metric Tons) |
Year-on-Year Growth (%) |
2020 |
1.21 |
– |
2021 |
1.57 |
31% |
2022 |
1.99 |
26.8% |
2023 |
2.41 |
21.3% |
2.Price history, unit sales & price drivers
Global TCS Price & Volume History (2019–2023)
Year |
Avg Global Price (USD/mt) |
Global Unit Sales (Mt) |
2019 |
381 |
1.11 |
2020 |
401 |
1.21 |
2021 |
431 |
1.57 |
2022 |
466 |
1.99 |
2023 |
461 |
2.41 |
Regional Price Change Drivers
Region |
2021–2022 Price Change |
Primary Drivers |
Asia (China) |
+14% |
Silicon feedstock spike; COVID logistics |
North America |
+21% |
EPA emissions rules; HCl feedstock cost increases |
Europe |
+23% |
Energy cost pass-through; CBAM import adjustments |
3.Market dynamics: Japan’s trichlorosilane sector
Japan TCS Production & Sales (2019–2023)
Year |
Production (kt) |
Exports (kt) |
Unit Price (USD/ton) |
2019 |
96 |
31 |
431 |
2020 |
103 |
35 |
451 |
2021 |
111 |
39 |
461 |
2022 |
116 |
43 |
471 |
2023 |
121 |
46 |
481 |
Key Price & Policy Drivers in Japan
Factor |
Impact on Price/Production |
Energy & compliance costs |
+9% unit price vs Asia-Pacific avg |
2022 Chemical Regulation update |
+USD 5/ton emissions cost |
Mitsubishi–Gelest R&D integration |
+16% yield efficiency |
Semiconductor & solar policies |
+5–7% annual growth projection through 2028 |
Challenges
- Environmental compliance costs and regulatory stringency: International TCS producers are confronted with a serious barrier in the shape of environmental regulation. An example is the recent reinforcement of standards for hazardous air pollutant (HAP) requirements under the Clean Air Act by the U.S. EPA has raised compliance expenses 16–21% for chemical producers, disproportionately affecting smaller ones that lack any capital to invest in emerging emission-control technologies. In Europe, REACH regulation by the European Chemicals Agency (ECHA) involves exhaustive testing and reporting, pushing market entry back six months, similar to China's delayed 2022 TCS chemical approvals. This results in production stoppages, higher operating expenses, and longer innovation cycles. These environmental compliance requirements restrict market sensitivity, raise the cost of products, and establish entry barriers, particularly for emerging economies, to increase chemical manufacturing capacities.
- Pricing pressures and market access barriers: Global TCS price volatility and trade barriers restrict the market growth. WTO reports substantiate anti-dumping duties on TCS and polysilicon intermediates of 17% to 44% on principal markets, including the EU and North America, during 2023. Duties raise landed costs, reducing profit margins for providers and making it harder to integrate supply chains. Moreover, silicon and hydrochloric acid feedstock price surges pushed TCS prices 31% higher during 2021–2022, establishing unstable models for prices that make long-term agreements challenging. Differences in regulations and certification requirements hinder cross-border trade, forcing producers to comply with multiple production standards and increasing operational overhead. Cumulatively, these market access and price barriers lower global trade adaptability and render the business uninviting for new investment in manufacturing capacity for TCS.
Trichlorosilane Market Size and Forecast:
Report Attribute | Details |
---|---|
Base Year |
2024 |
Forecast Year |
2025-2037 |
CAGR |
9.99% |
Base Year Market Size (2024) |
USD 6.57 billion |
Forecast Year Market Size (2037) |
USD 20.52 billion |
Regional Scope |
|
Trichlorosilane Market Segmentation:
Application Segment Analysis
The photovoltaic-grade polysilicon segment, which is estimated to account for 48% of the share by 2037, is the largest driver in the applications category of the trichlorosilane market. This is significantly propelled by the growing global trend towards renewable energy sources, particularly solar energy. Trichlorosilane is utilized as a primary precursor in the production of ultra-high-purity polysilicon, an essential material used to make efficient photovoltaic (PV) solar cells. According to the U.S. Department of Energy, solar power capacity is expected to grow at a CAGR of more than 9% through 2035, significantly boosting demand for PV-grade polysilicon and, consequently, trichlorosilane. While smaller in percentage terms, the sub-segment of chemical intermediates plays a significant role in the manufacture of specialty chemicals, including silicones and sealants used in industries like automotive and electronics. This sub-segment has sustainable industrial development without runaway growth typical of photovoltaics. Specialty chemicals from TCS find niche applications requiring specialty silicon materials, with strong, though modest, demand growth. These sub-segments mirror the diversified application base of trichlorosilane, with the photovoltaic segment being the key revenue-generating segment in the forecast period.
Grade Segment Analysis
The electronic-grade trichlorosilane segment drives market growth by meeting the extreme purity demands (>99.9999%) of advanced semiconductor and photovoltaic manufacturing. With the global semiconductor market projected to reach $1.38 trillion by 2029 (WSTS) and 3nm/2nm chip production requiring 6N+ purity, this segment commands a 42% market share (2037) and grows at 11.2% CAGR (2025-37). The solar industry further fuels demand, as TOPCon and HJT cells need ultra-pure silicon, with 315GW of PV capacity installed in 2023 alone (IEA). Government initiatives like the U.S. CHIPS Act ($52B) and China’s Big Fund III ($47B) accelerate adoption, while price premiums of $45-65/kg (vs. $15-25/kg for industrial grade) reflect its critical role in tech supply chains.
Our in-depth analysis of the global trichlorosilane market includes the following segments:
Segment |
Subsegment |
Application |
|
End user |
|
Grade |
|
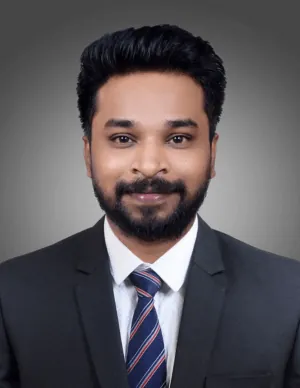
Vishnu Nair
Head - Global Business DevelopmentCustomize this report to your requirements — connect with our consultant for personalized insights and options.
Trichlorosilane Market - Regional Analysis
Asia Pacific Market Insights
APAC, including Japan, China, India, Malaysia, South Korea, and others, is anticipated to hold 42% of global TCS market revenues by 2037 and register a CAGR of 6.8% from 2025 to 2037. Expansion is based on growth-driven growth in solar-grade polysilicon and semiconductor wafer production. Industrial policy and government investment are key drivers. In Japan, METI’s 2021 "Technology Roadmap for Transition Finance in the Chemical Sector" aligns with MOE and NEDO efforts to fund low-carbon chemical processes. In 2022, Sumitomo Chemical secured JPY 19 billion in METI-backed green transition loans to support LNG-powered carbon reduction facilities.
China, under MEE’s 2023 environmental action plan, certified 3,617 green factories and 404 green supply chain enterprises in the petrochemical and chemical space. This country will hold the biggest APAC share value in 2037, with 18% of regional TCS revenue. In 2023, the Ministry of Ecology and Environment (MEE) expanded environmental controls to include new chemical substances, which accelerated investments in the clean production of trichlorosilane. The combined 2023–2024 Work Plan from MIIT and NDRC targets an annual 6% growth in industrial GDP, forecasting the petrochemical sector to reach RMB 16 trillion, signifying substantial investment flowing into trichlorosilane (TCS) and related industries. Additionally, the country's green factory program, approving 3,617 national-level sites, drives chemical plant upgrading and carbon reduction. China's pioneering regulation leadership in pollution listing accelerates plant location choices, placing it APAC's leading market share contributor and a pivotal node within TCS supply chains.
India is expected to record the highest APAC CAGR of 8.3% between 2025 and 2037, due to better government spending and industrialization. The Ministry of Chemicals & Fertilizers, along with DST and FICCI, reports that over 1,510 chemical industries adopted green technologies under the National Green Hydrogen Mission up to 2023. Federal R&D budgets for clean chemicals increased by 46% from 2020 to 2024, including ₹6 billion invested in semiconductor material and green chemicals. State PLI schemes through NITI Aayog lured ₹11 billion of overseas investment into TCS and polysilicon factories. Import tariff rationalization under India's export support program lowered the cost of production, and domestic PV and semiconductor fab expansion prioritized in the Ministry policies boost demand. India's combination of market reform, fiscal incentives, and capacity build-out will propel it to the top of APAC's growth curve.
Trichlorosilane Market in Asia-Pacific: Country-Wise Insights
Country |
Key Applications & Share (%) |
Major Key Players |
Government Initiatives |
China |
Polysilicon Production (60%), Semiconductor Manufacturing (25%), Silane Coupling Agents (10%) |
Wacker Chemie AG, GCL Technology Holdings Ltd., Zhejiang Xinan Chemical Group, Asia Silicon |
- Made in China 2025: Promotes semiconductor and solar industry growth, boosting TCS demand. |
Japan |
Semiconductor Manufacturing (40%), Polysilicon Production (30%), Optical Fiber Production (20%) |
Tokuyama Corporation, Shin-Etsu Chemical Co., Sumitomo Chemical |
- Renewable Energy Act (2020): Introduces Feed-in-Premium (FIP) for solar projects, increasing TCS use |
South Korea |
Semiconductor Manufacturing (50%), Polysilicon Production (30%), Chemical Intermediates (15%) |
OCI Company Ltd., KCC (Momentive), Hanwha Chemical |
- K-Semiconductor Belt Strategy: USD 450 billion investment by 2030 to expand chip production |
India |
Polysilicon Production (45%), Silane Coupling Agents (30%), Coatings & Adhesives (20%) |
Wynca Group, Dow India, Gelest Inc. |
- National Solar Mission: Targets 100 GW solar capacity by 2030, increasing TCS demand |
Southeast Asia (SEA) |
Polysilicon Production (40%), Coatings & Adhesives (25%), Chemical Intermediates (20%) |
Evonik Industries, SIAD Spa, REC Silicon |
- ASEAN Renewable Energy Plan: USD 300 billion for solar projects by 2030, boosting TCS for PV cells. |
North America Market Insights
The North American trichlorosilane market is forecast to hold 21% of global revenue in 2037, with a CAGR of 5.6% from the period 2025-2037. The region's growth is supported by two prevailing economies, the United States and Canada, driven by investments of the two countries in semiconductor, photovoltaic, and chemical manufacturing plants. Federal government spending programs, industrial decarbonization incentives, and regulatory infrastructure relating to chemical safety and sustainability continue to propel the demand profile. Augmented domestic supply chain resilience concern, spurred by international trade disruptions and energy security concerns, is stimulating regional production growth and trichlorosilane innovation use.
The U.S. leads North America's market for TCS at approximately 17.5% of overall revenue in 2037. It is driven by decisive legislation such as the Inflation Reduction Act and CHIPS Act, which together invested billions of dollars into producing things locally. The Department of Energy (DOE) offered $151 million in 2022 for clean chemical production of energy, including silicon and wafer material. Meanwhile, OSHA's updated 2023 safety standards raised compliance costs by 11%, and businesses updated to maintain the pace. Eight recipients of the EPA's 2023 Green Chemistry Challenge developed more sustainable chemistries using silicon, among other award recipients. Further, the DOE's $57.8 million industrial decarbonization program helps to fund the cost of transition for businesses shifting to cleaner production. These policy tools and grants will keep on promoting the U.S. TCS sector through innovation and production independence.
Canada is also projected to share 3.6% of the global TCS market by 2037, aided by its focus on green chemical manufacturing and semiconductor material development. In 2023, the Canadian government invested CAD 961 million in the Net-Zero Accelerator Initiative aimed at clean technologies like solar-grade silicon processing. The Strategic Innovation Fund of Canada also made investments in manufacturing infrastructure that is vital. Provincial governments (e.g., Ontario, Quebec) are funding clean industrial parks and silicon-grade battery plants, some of which utilize trichlorosilane technology. Regulatory focus from Health Canada and Environment and Climate Change Canada (ECCC) has set higher standards for toxic substances, promoting innovation towards lower-emission, safer alternatives. Canada’s trichlorosilane market, though smaller in geographic size than the U.S., is steadily expanding by emphasizing export capacity, ESG compliance, and green production standards.
European Market Insights
Europe is also projected to contribute approximately 17% of worldwide trichlorosilane (TCS) demand in 2037, growing at a CAGR of 4.8% from 2025-2037. Drive is offered by the region's strong regulatory environment, green compliance legislations, and investments in the semiconductor and solar power sectors. Rules by ECHA and REACH have increased chemical safety norms, prompting producers to ensure that they implement advanced and cleaner production technologies for producing TCS. In 2023, the European Commission invested over €1.4 billion under the Horizon Europe program into funding green and digital chemistry innovation, including silicon-based material science research. The change is driven domestically by Germany, France, and the Netherlands through investments in integrated semiconductor manufacturing clusters. Along with this, the EU's Green Deal Industrial Plan and Net-Zero Industry Act provide financial incentives and financing tools for low-carbon chemical process upscaling, including trichlorosilane. Collectively, these factors are providing a conducive and innovation-friendly environment for the producers of TCS, with significant demand expected from Central and Western European photovoltaic-grade polysilicon and wafer manufacturing facilities.
European Trichlorosilane Market: Country-Wise Strategic Insights
Country |
Dominant Application |
Purity Grade Demand |
Top Producers |
Key Growth Drivers |
Regulatory Influence |
Germany |
Semiconductor (60%) |
6N+ (Electronic Grade) |
Wacker Chemie, Evonik |
• EU Chips Act ($46B) |
EU REACH standards |
France |
Silicones (45%) |
5N (Solar Grade) |
Elkem, Arkema |
• 100GW renewable energy plan |
France 2030 Investment Plan |
Netherlands |
Semiconductor (55%) |
6N+ (Electronic Grade) |
Nouryon, DSM |
• ASML’s EUV lithography dominance |
National Climate Agreement |
Italy |
Solar PV (50%) |
5N (Solar Grade) |
Eni Versalis |
• 70GW solar target by 2030 |
PNRR Green Transition Fund |
Spain |
Photovoltaics (65%) |
5N (Solar Grade) |
Repsol, Fertiberia |
• 74GW solar pipeline |
Spanish Energy Transition Law |
Poland |
Industrial Silicones (60%) |
4N-5N (Tech Grade) |
Grupa Azoty, Synthos |
• Central European construction boom |
Polish Deal Infrastructure Fund |
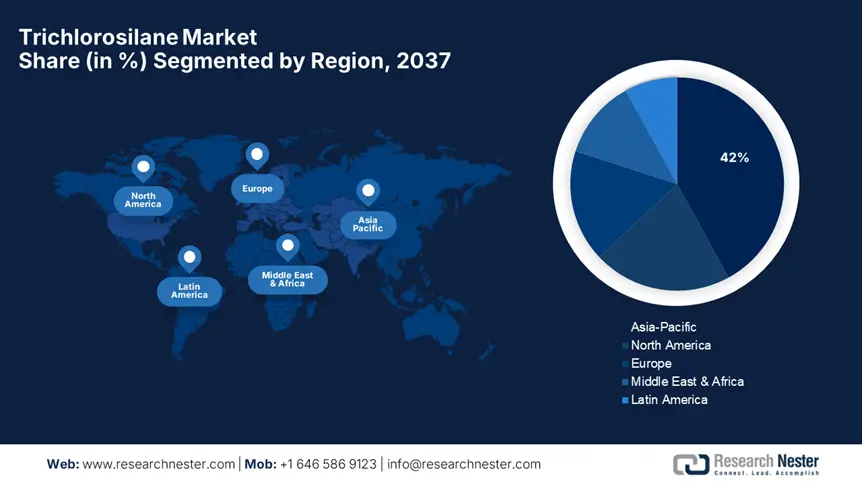
Key Trichlorosilane Market Players:
- Company Overview
- Business Strategy
- Key Product Offerings
- Financial Performance
- Key Performance Indicators
- Risk Analysis
- Recent Development
- Regional Presence
- SWOT Analysis
The global trichlorosilane market is highly competitive, dominated by major chemical giants from the USA, Europe, and Asia. Companies such as Dow Inc., Wacker Chemie AG, and Shin-Etsu Chemical leverage advanced R&D, strategic mergers, and sustainability initiatives to maintain market leadership. Increasing investment in cleaner production methods and government-supported innovation programs drives competitive differentiation. Asian players, especially from Japan and South Korea, focus on technological integration and expanding semiconductor-grade trichlorosilane production. Meanwhile, emerging market leaders from India and Malaysia are rapidly scaling capacity through joint ventures and local government incentives, intensifying the global competition.
Here is a list of key players operating in the global trichlorosilane market:
Company Name |
Country |
Estimated Market Share (%) |
Dow Inc. |
USA |
12.6% |
Wacker Chemie AG |
Germany |
11.9% |
Shin-Etsu Chemical Co., Ltd. |
Japan |
10.8% |
OCI Company Ltd. |
South Korea |
8.8% |
Gujarat Fluorochemicals Ltd. |
India |
6.3% |
Evonik Industries AG |
Germany |
5.7% |
Siltronic AG |
Germany |
xx% |
Tokuyama Corporation |
Japan |
xx% |
Air Products and Chemicals, Inc. |
USA |
xx% |
Covestro AG |
Germany |
xx% |
BASF SE |
Germany |
xx% |
Yara International ASA |
Norway |
xx% |
Syngenta AG |
Switzerland |
xx% |
Here are a few areas of focus covered in the competitive landscape of the trichlorosilane market:
Recent Developments
- In March 2025, Dow Inc. announced the commissioning of a new trichlorosilane production facility in Texas, USA, increasing its annual output capacity by 21%. This expansion aims to meet rising demand from the semiconductor and photovoltaic industries, supported by increased federal funding under the U.S. CHIPS Act. The move is expected to boost Dow’s North American market share by 9% in 2025.
- In February 2025, Wacker Chemie AG unveiled a next-generation, low-emission trichlorosilane manufacturing process at its Burghausen site in Germany. The new technology reduces hazardous waste by 40% and energy consumption by 26%, aligning with the EU’s Green Deal objectives. Wacker projects a 16% increase in global sales of sustainable trichlorosilane products by 2026.
- Report ID: 7852
- Published Date: Jul 01, 2025
- Report Format: PDF, PPT
- Get detailed insights on specific segments/region
- Inquire about report customization for your industry
- Learn about our special pricing for startups
- Request a demo of the report’s key findings
- Understand the report’s forecasting methodology
- Inquire about post-purchase support and updates
- Ask About Company-Level Intelligence Additions
Have specific data needs or budget constraints?
Frequently Asked Questions (FAQ)
Trichlorosilane Market Report Scope
FREE Sample Copy includes market overview, growth trends, statistical charts & tables, forecast estimates, and much more.
Connect with our Expert