Japan Market Size, Forecast, and Trend Highlights Over 2025-2037
Japan Turbo Compressor Market size was valued at USD 303.4 million in 2024 and is projected to reach a valuation of USD 599.6 million by the end of 2037, rising at a CAGR of 5.3% during the forecast period, i.e., 2025-2037. In 2025, the industry size of japan turbo compressor is estimated at USD 319.7 million.
Japan turbo compressor market is witnessing steady expansion as a result of decarbonization policies and the modernization of infrastructure. Companies are concentrating on localized R&D to comply with industrial and environmental standards. In December 2024, Mitsubishi Heavy Industries launched single-shaft turbo compressors through digital twin simulations that were tested in Hiroshima. This design improves the performance forecasting of complex refinery arrangements. Growth is sustained with government-led energy initiatives and revived domestic capacity investment. The continued trend towards smart, automated systems continues to strengthen japan turbo compressor market uptake among verticals.
The governmental strategic efforts also affect adoption trends. New guidelines on the promotion of oil-less compressors in water treatment systems were introduced in March 2025 by the Ministry of Environment. These guidelines facilitate energy saving and reduce contamination during operation. The urban municipalities have started pilot deployments, which is an indication of increased institutional involvement. The overall sustainability drive is supported by long-term rewards such as Japan’s carbon neutrality roadmap. OEMs are riding on this momentum to realign portfolios with regulatory needs. With the differentiation of demand, energy-efficient application-specific compressors are garnering rapid demand.
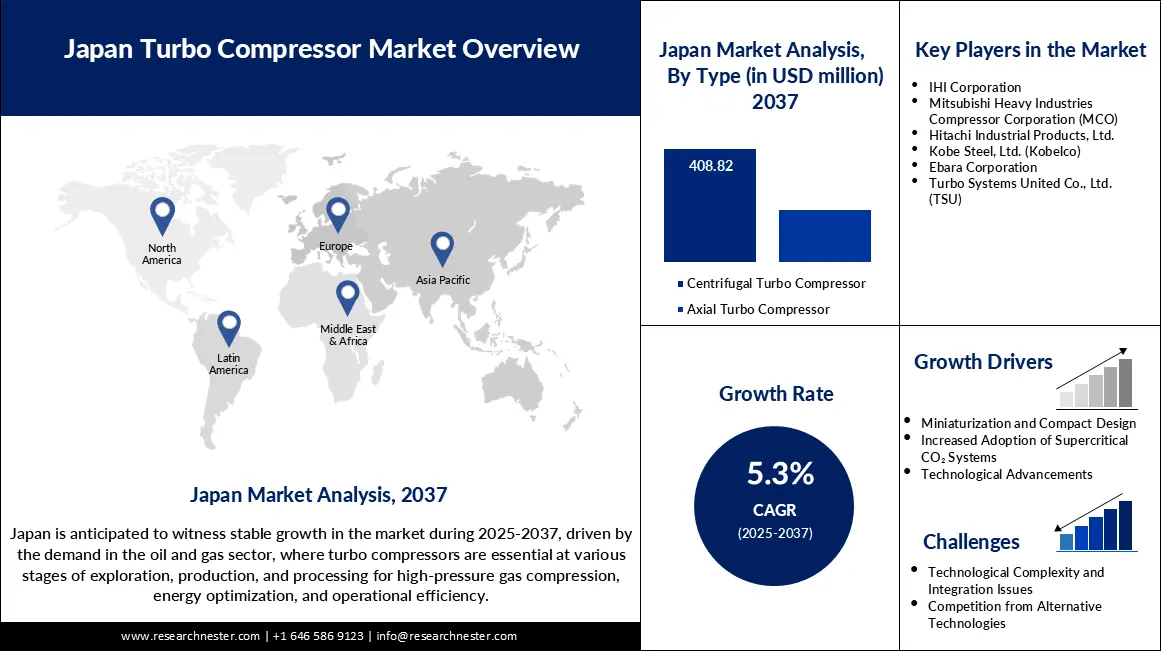
Japan Turbo Compressor Sector: Growth Drivers and Challenges
Growth Drivers
- Digital transformation and smart systems: Digital transformation continues to be a key growth lever in Japan’s turbo compressor industry. In January 2024, Hitachi incorporated AI-powered diagnostics in its Lumada platform for compressor units. This innovation is capable of supporting predictive maintenance and anomaly detection in real time. With the manufacturing sector in Japan moving towards Industry 4.0, smart compression systems are picking up pace. These systems also comply with the national automation objectives of the Connected Industries initiative. The attraction is the decreased downtime, operational transparency, and adaptive performance tuning.
- Carbon neutrality and specialized compressors: Carbon neutrality objectives are driving OEMs to invest in special compressor systems. In August 2024, Mitsubishi Heavy Industries increased the production of MAC-series compressors that can handle COâ‚‚ at 10,000 psi. These units serve carbon capture needs in refineries and gas storage locations. The technology aligns with Japan’s shift to carbon recycling and sequestration. This segment is receiving policy attention with the 2050 net-zero target. As the industry changes, high-pressure and environmentally compliant systems are becoming the norm.
- Hydrogen infrastructure and clean fuel networks: Hydrogen infrastructure is defining new investment avenues. In September 2024, Kobe Steel launched high-pressure centrifugal compressors designed for ammonia and hydrogen applications. Such systems are connected to clean fuel networks and have ultra-low temperature requirements. The government’s energy diversification roadmap reinforces this need. When hydrogen and ammonia establish their place in power generation, compression technology for the concerned industry gets more R&D money. This trend places the hydrogen segment as a high-potential growth segment.
Challenges
- Strict noise compliance in urban areas: One challenge in the Japan turbo compressor market is strict noise regulations in urban areas, with mandatory limits implemented in October 2024 for compressors in noise-sensitive locations. This forces OEMs to develop innovative housing designs and dampening technologies for acoustic control, potentially affecting product margins. These advancements are crucial for meeting the specific demands of urban environments. As such, OEMs have to invest in research and development in order to design quiet but high performing compressors to comply with such regulations.
- Regulatory standardization across global markets: Another challenge for the japan turbo compressor market is the standardization of regulation in global markets, with Japan harmonizing JIS B 8341 testing standard with ISO 5389 in January 2024, necessitating redesign efforts on behalf of OEMs to conform to the international protocols, and adding complexity for manufacturers of both domestic and overseas japan turbo compressor markets, pressuring smaller firms As a result, manufacturers need to be proactive to keep up with changing global standards to remain competitive.
Japan Turbo Compressor Market: Key Insights
Report Attribute | Details |
---|---|
Base Year |
2024 |
Forecast Year |
2025-2037 |
CAGR |
5.3% |
Base Year Market Size (2024) |
USD 303.4 million |
Forecast Year Market Size (2037) |
USD 599.6 million |
Regional Scope |
|
Japan Turbo Compressor Segmentation
Type (Centrifugal Turbo Compressor, Axial Turbo Compressor)
The centrifugal turbo compressor segment is expected to lead the japan turbo compressor market, accounting for 68% share during the forecast period. This type is preferred due to its compactness, increased efficiency in continuous operations, and ability to be used in various industries. In February 2024, LG Chem’s HVO facility in South Korea placed an order for a centrifugal compressor with Hitachi. Designed and manufactured in Japan, the project increased exposure for Japan’s energy-efficient compressor technologies. Massive use in the oil, gas, and clean energy industries further consolidates its japan turbo compressor market lead.
The centrifugal models are gaining significant traction in LNG and hydrogen-related projects. Their low maintenance needs and scalable architecture make them appealing for continuous load operations. Japanese OEMs are also incorporating digital layers for smarter operation. In July 2024, Ebara added Elliott’s digital control systems to its compressors in order to optimize performance in LNG terminals. These systems increase uptime and life cycle cost reduction, enhancing centrifugal dominance.
Stage (Single-Stage, Multi-Stage)
Multi-stage turbo compressors are anticipated to account for 70% share of the japan turbo compressor market by 2037. These compressors offer greater pressure ratios, thereby suitable for industrial processes such as petrochemical production and hydrogen compression. In December 2024, METI approved subsidies for multi-stage compressors for COâ‚‚ capture applications. The focus was on systems with high gas reinjection abilities. Such applications need exact pressure control, which proves the worth of the multi-stage section.
For operational reliability and redundancy, industries are increasingly preferring multi-stage systems. With regulations heating up concerning safety and efficiency, the ability to fine-tune operations across stages is critical. In May 2024, Hitachi added dual-redundant leak detectors and auto shutdowns to their compressor line to conform to Japan’s High-Pressure Gas Safety Act. These enhancements cater to high-pressure settings common for the multi-stage designs and contribute to adoption.
Application (Oil & Gas, Steel Plant, LNG Terminal, Hydrogen & Ammonia Fuel Power Generation, COâ‚‚ & Air Storage Power Generation, Others)
The oil & gas segment is projected to account for 40.0% of the japan turbo compressor market share through 2037. This industry needs strong compression technology for refinery, gas processing, and enhanced oil recovery. In December 2024, Mitsubishi Heavy Industries tested steam turbine-driven compressors in its Hiroshima plant for a U.S. ethane cracker. Despite being intended for export, the development highlights Japan’s role in providing high-performance units. Domestic refineries also continue to require customized, durable systems.
The growth of the segment is also driven by Japan’s energy security objectives and the stable investments into gas infrastructure. Existing assets are being modernized, which is leading to compressor upgrades. In August 2024, the Ministry of Land, Infrastructure, Transport, and Tourism approved LNG terminal retrofits with smart turbo compressors. Yokohama and Osaka ports began procurement rounds. These projects highlight the continued requirement for high-quality compression in the oil & gas supply chain.
Our in-depth analysis of the global japan turbo compressor market includes the following segments:
Type |
|
Stage |
|
Capacity |
|
Power Output |
|
Speed |
|
Application |
|
Companies Dominating the Turbo Compressor Landscape
- IHI Corporation
- Company Overview
- Business Strategy
- Key Product Offerings
- Financial Performance
- Key Performance Indicators
- Risk Analysis
- Recent Development
- Regional Presence
- SWOT Analysis
- Mitsubishi Heavy Industries Compressor Corporation (MCO)
- Hitachi Industrial Products, Ltd.
- Kobe Steel, Ltd. (Kobelco)
- Ebara Corporation
- Turbo Systems United Co., Ltd. (TSU)
Japan turbo compressor market is highly competitive, characterized by innovation and strong domestic players. Some of the top manufacturers are IHI Corporation, Mitsubishi Heavy Industries Compressor Corporation, Hitachi Industrial Products, Kobe Steel, Ebara Corporation, and Turbo Systems United. These companies are not only competing in the local japan turbo compressor market but also looking to venture into the APAC and global infrastructure markets. R&D, compliance readiness, and integration of smart technologies are their strong points. Differentiation is more and more oriented towards efficiency, flexibility, and digitalization.
Mitsubishi Heavy Industries introduced IoT-driven turbo compressors for the intelligent use of utilities in November 2024. The system is designed for Japanese power firms and chemical plants and includes automated shutdown and real-time analytics. The move signals MHI’s dedication to smart manufacturing and fits in with national energy resilience objectives. Competitors are also moving in this direction by incorporating similar capabilities, and smart functionality is becoming a new standard in competitive differentiation.
Here are some leading companies in the Japan turbo compressor market:
Recent Developments
- In October 2024, Ebara’s Elliott brand launched new centrifugal compressors tailored for LNG and refining. Manufactured in Japan, they support high-capacity, energy-efficient operations. The models are equipped with VFD control and oil-free design options. They strengthen Ebara’s ESG-focused "E-Vision 2030" global strategy.
- In June 2024, IHI Corporation’s Japan-based team designed a compact electric turbo compressor using air-bearing technology. It delivers 100 kW and is used in fuel cell systems and sustainable aviation. This development enhances Japan’s leadership in lightweight, zero-emission compressors. The innovation triples output compared to IHI’s prior generation units.
- In March 2024, Hitachi developed high-efficiency centrifugal compressors with advanced impeller designs. These systems cater to Japan’s petrochemical, chemical, and gas industries. The products contribute to Hitachi’s long-term environmental goals. They also improve thermal stability and performance in industrial settings.
- Report ID: 7681
- Published Date: May 19, 2025
- Report Format: PDF, PPT
- Get detailed insights on specific segments/region
- Inquire about report customization for your industry
- Learn about our special pricing for startups
- Request a demo of the report’s key findings
- Understand the report’s forecasting methodology
- Inquire about post-purchase support and updates
- Ask About Company-Level Intelligence Additions
Have specific data needs or budget constraints?
Frequently Asked Questions (FAQ)
Japan Turbo Compressor Market Report Scope
FREE Sample Copy includes market overview, growth trends, statistical charts & tables, forecast estimates, and much more.
Connect with our Expert